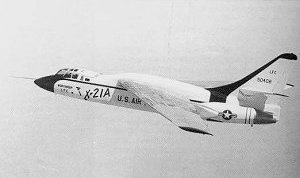
The X-21A had thousands of tiny holes in the skin of its wings, through which air was pumped, to study the boundary layer.
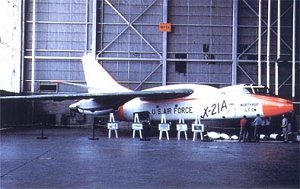
Inside the X-21A was an incredible array of electronics and wiring, to control the airflow, as well as to record data.
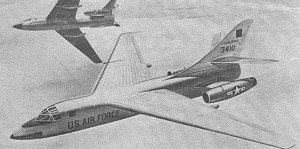
Early
published painting lacked the characteristic dorsal bump.
(image courtesy of Paul Duplessis, B66.info webmaster)
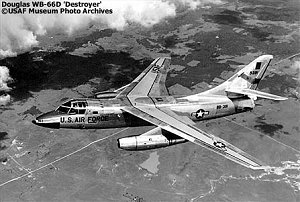
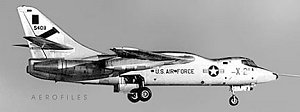
Although
the parenthood of the original WB-66D design (top) was obvious in a side
view of the X-21, a bottom view clearly shows how different the two aircraft
reallywere.
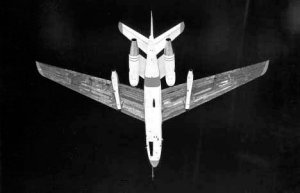
With a completely new wing and engine nacelles that were hung on either side of the aft fuselage, the two X-21As did not much resemble the Douglas WB-66D (AFFTC History Office)
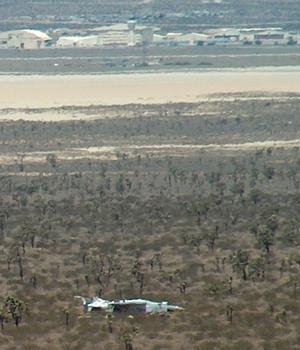
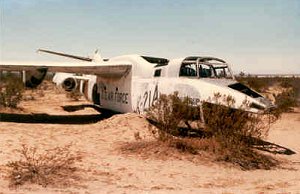
The X-21As are currently rotting in Edwards' desert photo area.
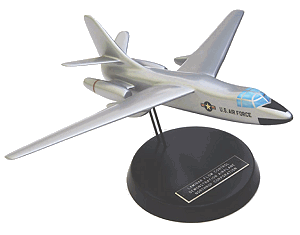
(1) Work on drag reduction by means of increasing the laminar flow by boundary layer suction was first performed at Langley Aeronautical Laboratory in the late 1930's by Albert E. Doenhoff and Ira H. Abbott. Laminar-flow control is a technology that offers the potential for significant improvement in drag cooefficient which would provide improvements in aircraft fuel usage, range or endurance that far exceed any known single aeronautical technology. In principle, if 80% of wing is laminar, then overall drag could be reduced by 25%. The frictional force between the air and the aircraft surface, known as viscous drag, is much larger in a turbulent boundary layer than in a laminar one. The principal type of active laminar-flow control is removal of a small amount of the boundary-layer air by suction through porous materials, multiple narrow surface slots, or small perforations.
|
 |
NORTHROP LFC
USAF designation: X-21A, X-21B
Powerplant: 2x 9,400
lbf (41.9 kN) General Electric J79-GE-13
First flight (first prototype): 18 April 1963 (p: Jack Wells)
First flight (second prototype): 15 August 1963 (p: Jack Wells)
NASA became aware in 1960 of a renewed USAF interest in active laminar-flow control1 through a visit of Philip P. Antonatos of the USAF Wright Air Development Division (WADD) to Albert L. Braslow, who was then head of the General Aerodynamics Branch of the Langley Research Center (LaRC) Full-Scale Research Division. Contemplated Air Force missions at that time included a high-altitude subsonic aircraft of long-range and endurance, an ideal match with laminar-flow control. Laminar flow was required to obtain the long range or endurance and high altitude alleviated the adverse effects of surface protuberances. Any special operational needed to maintain the required surface smoothness in the presence of material erosion and corrosion and to cope with weather effects, aircraft noise, and the accumulation of dirt and insects could only be evaluated through actual flight experience. WADD also considered it important to provide an impressive flight demonstration of improved airplane performance to be better able to advocate the advantages of the contemplated new aircraft. A flying testbed was therefore needed that would be devoted to boundary layer control research in wing design.
On 4 June 1961, The Northrop Corporation disclosed the existence of a "porous wing" plane under development for USAF, which was in fact modified version of WB-66D proposed by the WADD and based on the inhalation concept (eliminating up to 80 percent of the frictional drag) proposed by Werner Pfenninger. Using modified WB-66D airplanes implied minimum cost, high degree of safety, and short development time. Under sponsorship of the Air Force (with a monetary contribution from the Federal Aviation Administration), Northrop modified the airplanes with slotted suction wings and designated them as experimental aircraft X-21A LFC and X-21B LFC, the second aircraft differing only in de-icing and added test equipment. A third frame [55-0409] was scheduled, but was damaged in delivery and therefore never completed. The B-66 fuselage was modified with the
wing-mounted engines moved to the rear fuselage and making space for air compressors. A large hump was added on the top of the fuselage, with additional modifications to laminar flow exhausts, and tail cone. Slots were incorporated in the wing's surface to inject air into the boundary layer, inducing non-turbulent laminar air-flow.
Paper and wind tunnel studies conducted by Northrop had indicated boundary layer control would offer numerous
performance benefits. The X-21A was fitted with a completely new wing of increased span and area, with a sweep reduced from 35 degrees to 30 degrees. The wing had a series of span-wise slots through which turbulent boundary-layer was sucked away, resulting in a smoother laminar flow operation, hopefully resulting in reduced drag, better fuel economy, and longer range. The underwing podded J71 engines were removed and replaced by a pair of 9490 lb.s.t General Electric XJ79-GE-13 turbojets mounted in pods attached to the rear of the fuselage sides. Bleed air from the J79 engines was fed into a pair of underwing fairings, each of which housed a bleed-burn turbine which sucked the boundary layer air out through the wing slots. The forward cockpit carried a pilot and two flight engineers. Two additional flight test engineers were housed in a central fuselage bay underneath the wing. Testing proved that the overall concept was feasible, and a substantially improved range was obtained. However, it was found essential to keep the tiny wing slots spotlessly clean for effective operation, and this and other maintenance difficulties made the concept too costly for practical applications.
The X-21A was eventually to show some benefits, but these benefits came at a significant
maintenance penalty: practical application of the concept initially proved unworkable, since rain, dirt, dust, bugs and other particulates clogged the slots. Northrop began flight research in April of 1963 at Edwards Air Force Base. Several problems arose early in the project that consumed significant periods for their solution. Principal among these were surface smoothness problems, an unexpected severity of a spanwise contamination problem and the use of porous materials. With respect to the smoothness problem, in spite of a concerted effort to design and build the slotted wings for the two airplanes to the close tolerances required, the resulting hardware was not good enough. Discontinuities in spanwise wing splices were large enough to cause premature transition to turbulent air flow. Putty, used to fair out these discontinuities, chipped during flight with resulting roughness large enough to trigger transition from laminar to turbulent flow.
The combination of X-21 wing geometry, flight altitudes, and Mach numbers was such that local turbulence at the attachment line, e.g., from the fuselage or induced by insect accumulation, caused turbulent flow over much of the wing span. With the large-scale X-21 flight tests and further wind-tunnel tests, Northrop developed methods for avoidance of spanwise contamination. Another problem that was uncovered during the X-21 flight tests was associated with ice crystals in the atmosphere. Researchers noted that when the X-21 flew in or near visible cirrus clouds, laminar flow was lost. In certain conditions, ice crystals would form due to the rapid cooling of air over those laminar surfaces abruptly disrupting laminar flow; however, upon emergence from the ice crystals, laminar flow was immediately regained through rapid melting of the ice. Northrop developed a theory to indicate when laminar flow would be lost as a function of atmospheric particle size and concentration.
By October of 1965, attainment of "service experience comparable to an operational aircraft," one of the program's principal objectives, had not even been initiated because of the effort absorbed by the previous problems. To proceed with this initiative, the advisors to the Air Force recommended that a major wing modification would be needed before meaningful data on service maintenance could be obtained. This, unfortunately, was never done because of various considerations at high levels of the Air Force, probably predominantly the resource needs of hostilities in Vietnam. Much extremely valuable information, however, was obtained during the X-21 flight program, supported by wind-tunnel and analytical studies.
After successfully demonstrating the ability to achieve laminar flow over approximately 75
percent of the wing surface, the X-21As were used to explore the impact of rain, sleet, snow, and other weather
anomalies on the system.
During the flight test program, the X-21As demonstrated that the boundary layer control technique, called laminar
flow control, was both effective and viable. At the end of the program, 38 flights attained laminar flow on a fairly large airplane over 95 percent of the area intended for laminarization. Unfortunately, top management in government and industry remembered the difficulties and time required to reach this point more than they did the accomplishment. The last known location of both X-21's was Edwards AFB, where they had been gutted of most instrumentation and left out of doors to deteriorate. Their legacy is not lost however, since the data accumulated was helpful in later LFC-oriented programs such as the F-111 TACT or the F-16XL.
Population: 2 [55-0408, -0410] (B-66 registrations)
Specs:
Length: 75 ft 2.5 in (22.9 m)
Height: 25 ft. 6 in. (7.7 m)
Wingspan: 93 ft. 6 in. (28.51 m)
Wingarea: 1,250.0 sq. ft. (116.1 sq.m)
Empty Weight: 45,828 lb (20,783 kg)
Gross Weight: 83,000 lb (37,641 kg)
Performance:
Range: 4,780 miles (7,697 km)
Maximum achieved speed: 560 mph (901 km/h, 487 kt)
Cruising speed: 560 mph (896 km/h)
Service ceiling: 42,500 ft (12,957 m)
Crew/passengers: 5
Main sources:
- Albert
L. Braslow's book on Laminar-Flow Control
- Joe Baugher's X-21A page
- Wikipedia article on the
X-21
- X-Planes Data Site
|